Maintain Injury-Free Jobsites Through Digital Compliance Processes
By: Travis Parigi, Contributor
Many employers with field service teams have traditionally relied on the honor system for much of their safety and regulatory compliance. This can be a recipe for disaster that puts undue pressure on field technicians to take safety risks.
For example, a worker sent to run wiring at a client’s remote jobsite discovers that a power winch needed to pull cable bundles is damaged and unsafe. The individual knows they should stop to obtain a replacement or repair the winch before continuing—losing half a day to drive to their workshop and return to the site. Will they attempt to repair or continue to use the damaged tool to avoid the delay? Is the worker adequately trained and certified to recognize the danger or to perform the repair? Did other technicians know the winch was damaged or due for service, but fail to schedule its repair or replacement?
This hypothetical scenario underscores common challenges. In fact, equipment failure and machinery issues are among the most frequently cited OSHA violations. In addition to fines, these accidents can lead to serious financial losses related to an injury or death, as well as damage to the company’s reputation and employee morale.
The Right System
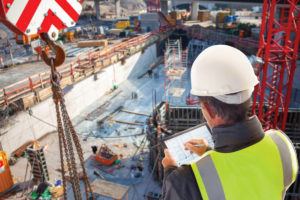
Many employers with field service teams have relied on the honor system for much of their safety and regulatory compliance. This can be a recipe for disaster that puts undue pressure on field technicians to take safety risks. (photo courtesy Adobe Stock)
A better approach is to enforce safety and regulatory compliance systematically using enterprise asset management technology (EAM). With the right systems in place, an organization can increase visibility into the condition of its equipment and machines; ensure workers are qualified for the jobs they are assigned to do; and maximize asset performance through predictive and proactive maintenance.
Today’s EAM platforms tackle compliance on multiple fronts. For an organization integrating one of these technology sets with its legacy systems, the first step toward greater efficiency typically is to modernize its job safety data and analyses through digitization.
Digital information is almost instantly retrievable and allows automation of many processes that can be tedious and prone to human error when performed manually. Once equipment records and ongoing reporting are converted to this more versatile format, safety managers and field service teams can quickly search and group that information to clarify worksite safety conditions.
Returning to our earlier example, the field technician’s quandary might have been avoided, if the worker had learned before setting out for the client’s worksite that the winch was damaged on a previous job or simply due (or overdue) for replacement. Drawing from previous reporting, manufacturer’s recommendations and specifications, and other key details stored in an EAM’s digital database, technicians can identify which machines and equipment are most reliable; which are failing or at risk of failing; and even where a specific tool, machine or vehicle is stored.
Over time, a platform can provide additional analytical insight by identifying trends and patterns that can inform predictive equipment maintenance and replacement. The previous life-
cycle of wear parts, for example, can tell planners when a motor’s brushes, contactor or other components are likely to need replacement. Notification functions can alert a purchasing officer in sufficient time to order replacement parts, so they are on hand when it comes time to service the machine. Digital inventory tracking also assists technicians in locating and pulling those parts, avoiding redundant purchases of components already in inventory.
Employee Coordination
Employers can use a similar approach to digitally track employee certifications. Just as a platform reveals a machine’s service history, software can keep managers updated on each worker’s training history and current certifications to perform various types of jobs. By tying certification tracking to assignment schedules and dispatching systems, supervisors and dispatchers can avoid sending out a journeyman to perform a job that will exceed their skillset or certifications, and should instead be performed by a specialist or a master electrician.
An EAM platform can incorporate and coordinate training histories with relevant contextual data, such as insurance requirements and upcoming dates when an individual must complete refresher courses or renew their certification. In practice, scheduling software can suggest a roster of available workers qualified to perform a needed task. A platform can also alert a dispatcher when a service team lacks certification for a task within an assigned job.
Predict and Prevent
Finally, a digital foundation positions a field service provider to institute systematic predictive and preventive maintenance. Leading EAM systems not only coordinate, but automate, many key administrative functions to maximize efficiency. In addition to scheduling inspections and service dates for thousands of pieces of equipment, a platform can automatically generate work orders and alerts in accordance with usage meters, or when triggered by events that would require a status check or repair.
In short, today’s EAM solutions remove the guesswork from safety and regulatory compliance. By continually tracking employee qualifications, a good platform enables managers to avoid placing building engineers and other service team members in positions for which they lack the proper training or certification needed to complete their tasks safely. By the same token, systems that track the upkeep and predict the performance of machinery and equipment help to minimize breakdowns, the risk of injuries and downtime due to unplanned repairs. Compliance becomes not a burden—but a means to achieving greater efficiency and worksite safety.
[Travis Parigi is Founder and CEO of LiquidFrameworks.]
Share on Socials!
Preventing Fire & Dust Explosions: NFPA 654
Safe Confined Space Entry for Cement Silos and Hoppers
Age “Correction” in Hearing Conservation Programs
Leaders in Industrial Hygiene
Council for Accreditation in Occupational Hearing Conservation (CAOHC)
Subscribe!
Sign up to receive our industry publications for FREE!